A feasibility study is a trial run that tests your manufacturing steps, materials, and equipment to confirm that your process is designed correctly. During a feasibility study, any differences in the process resulting from the scale, materials, or equipment differences will be exposed. Identified Critical Process Parameters (CPP) may need to be adjusted. The knowledge gained during a feasibility study will help mitigate the risks before submission to regulatory agencies or Process Performance Qualification (PPQ) batches.
Why a Feasibility Study is Important; Is a Feasibility Study Optional?
Many aspects need to be considered when you are looking to transfer your product with a CDMO partner. Feasibility study batches should be run to challenge critical manufacturing parameters and equipment differences.
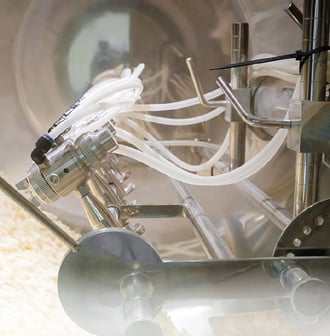
The purpose of a feasibility study is to produce similar product quality in a different equipment train or batch size during product transfer. Sometimes, it is quite challenging to achieve that goal. Although the operating principle of equipment is similar; the parameters setting may be totally different and depends on the brand of equipment used. For this reason, a feasibility study is important to ensure the manufacturing process parameters are suitable with your CDMO’s equipment.
Prior to the 2011 release of the FDA guidance on process characterization, the pharmaceutical industry historically viewed process characterization, the validation of a manufacturing process to minimize risk and ensure consistent quality throughout a product’s life cycle, as optional. Nowadays, a feasibility study is regarded as an essential step of drug development or product transfer. This is related to various benefits of feasibility studies, such as enhancing not only process understanding but also, and most importantly, patient safety.
What Does a Good Feasibility Study Plan Look Like?
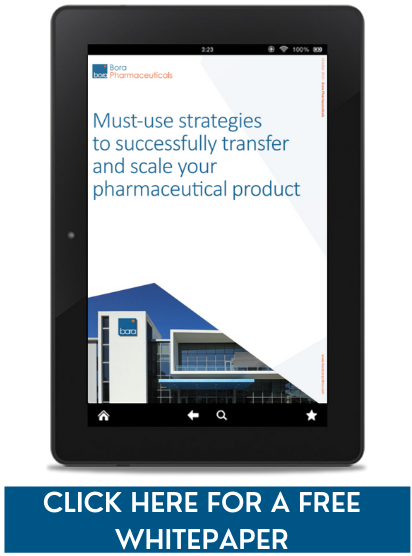
A good feasibility plan is a must to make sure the feasibility study runs efficiently and thoroughly. First of all, a comprehensive technical data package provided by the client is important. Your CDMO partner needs to review the data package carefully and discuss with your Research and Development or Technical Services team to understand the critical quality attributes (CQAs) and critical process parameters (CPPs). A feasibility study plan should be designed according to the information and discussions between you and your contract manufacturer
A feasibility study should start from a small scale, if applicable; to identify the parameter ranges in an economical way. Small scale feasibility studies can provide valuable feedback in determining and optimizing critical process parameters such as product temperature, mixing times, or compression speed. Feasibility studies confirm the right parameters needed to manufacture a given product consistently.
It is also encouraged putting samples from feasibility batches in an accelerated stability chamber for at least three months. The stability data can reveal if the product is stable or identify any potential adverse trend.
The key takeaway is to have a good feasibility plan that clearly defines the objectives of your project.
How Many Feasibility Study Batches Do You Need to Complete?
There is no magic number to decide how many feasibility study batches are required. It depends on the complexity of the process, the equipment differences between the two sites, or any product-specific requirement. “One-time success approach” and “Risk and science-based approach” are common approaches to be utilized during the product transfer.
One Time Success Approach
It means minimizing the number of feasibility study batches (usually just one small batch). The advantage is that it can potentially lead to a shorter tech transfer timeline to complete the submission or PPQ, and lower product transfer cost.
However, regulatory authorities may have concerns and request more information during the review of the filling document. These concerns may lead to manufacturing extra batches to the challenge and confirm the process parameters. If normal operating parameters are not verified; additional cost at a commercial scale is likely to happen (e.g. rejection of commercial batches due to unstable process).
Risk and Science-Based Approach Preferred
This approach is when feasibility study runs are based on the risk assessment and scientific justification. The advantage is that the overall lead time may be shorter than the “one-time success approach” due to a delay-free filling approval; rare deviations in commercial batches (even zero bad batches!); data from feasibility study batches can support once any deviation occurred in the commercial batches. Although the overall project lead time may be a little bit longer and the cost is higher than the “One time success approach”, you can expect the project to proceed on schedule. It can also avoid any short supply due to unstable product quality after commercialization.
Case Study: Controlling Processing Temperature for a Solvent-based Hot Melt Granulation Product
Bora just completed a product transfer project for a US-based client where they received an FDA Complete Response Letter based on a Prior Approval Supplement (PAS) filling for an oral solid dose product.
It was an extended-release product with a complex manufacturing process. It used a hot-melt granulation process with a solvent solution. The key was to control the product temperature during the granulation process to achieve the desirable dissolution profile.
Bora received the comprehensive technical document from the client and proposed the study plan with a risk and science-based approach. It started from the small feasibility study batches in a Glatt 60. The ranging study was conducted systematically to establish the operating ranges for critical process parameters. Although Bora encountered some issues during small-scale study batches, those issues were fixed before commercial-scale batches with the Glatt 300 and it reduced the waste efficiently.
For example, at the small-scale study batches, Bora manufactured the larger granules after the granulation process comparing them to the ANDA product and they failed to meet specifications. Moreover, we experienced sticking and scuffing issues after the coating process. Bora not only adjusted the process parameters and learned knowledge at small-scale batches but provided the Engineering solutions to overcome the issues. Those issues were solved effectively at a small scale and the PPQ batches were completed successfully without similar issues.
A Feasibility Study IS an Important Step in a Product Transfer!
A feasibility study is an essential step for product transfer. It can help to establish the control strategy and eliminate the risk before the submission or PPQ batches. By adopting and appropriately executing a scientific and risk-based approach that efficiently gathers the information you need to gain the best scientific output for patients. Your CDMO partner should have the capacity to propose an efficient and systematical feasibility plan to make sure to deliver a high-quality, effective drug in today’s competitive market.